Pinnatöötluse valik on probleem, millega iga disainer silmitsi seisab. Saadaval on mitut tüüpi pinnaravivõimalusi ja kõrgetasemeline disainer ei peaks mitte ainult arvestama disaini majanduse ja praktilisusega, vaid pöörama tähelepanu ka montaažiprotsessile ja isegi keskkonnavajadustele. Allpool on lühike sissejuhatus kinnitusdetailide jaoks, mis põhinevad ülaltoodud põhimõtetel, kinnitusdetailid.
1. Elektrogalvaniseerimine
Tsink on kaubanduslike kinnitusdetailide jaoks kõige sagedamini kasutatav kate. Hind on suhteliselt odav ja välimus on hea. Tavaliste värvide hulka kuuluvad must ja sõjaline roheline. Selle korrosioonivastane jõudlus on siiski keskmine ja selle korrosioonivastane jõudlus on madalaim tsingiplaadi (katte) kihtide seas. Üldiselt viiakse galvaaniseeritud terase neutraalne soolapihusti test läbi 72 tunni jooksul ja ka spetsiaalseid tihendusaineid kasutatakse tagamaks, et neutraalne soolapihusti test kestab enam kui 200 tundi. Hind on aga kallis, mis on 5-8-kordne tavaline tsingitud terast.
Elektrogalvaniseerimisprotsess on kalduvus vesiniku omastamisele, nii et polte, mis ületavad astme 10.9, ei ravita tavaliselt galvaniseerimisega. Ehkki vesinikku saab pärast plaadistamist ahju abil eemaldada, kahjustatakse passiivse kile temperatuuril üle 60 ℃, seetõttu tuleb vesiniku eemaldamine läbi viia pärast elektroplaani ja enne passiivsust. Sellel on halb töövõime ja kõrged töötlemiskulud. Tegelikkuses ei eemalda üldised tootmisettevõtted vesinikku aktiivselt, kui konkreetsete klientide volitused ei ole.
Tsingitud kinnitusdetailide pöördemomendi ja enne pingutamise jõu konsistents on kehv ja ebastabiilne ning neid ei kasutata tavaliselt oluliste osade ühendamiseks. Tormomendi eelkoormuse järjepidevuse parandamiseks saab määrimisvahendite katmise meetodit pärast plaadistamist kasutada ka pöördemomendi eelkoormuse järjepidevuse parendamiseks ja parandamiseks.
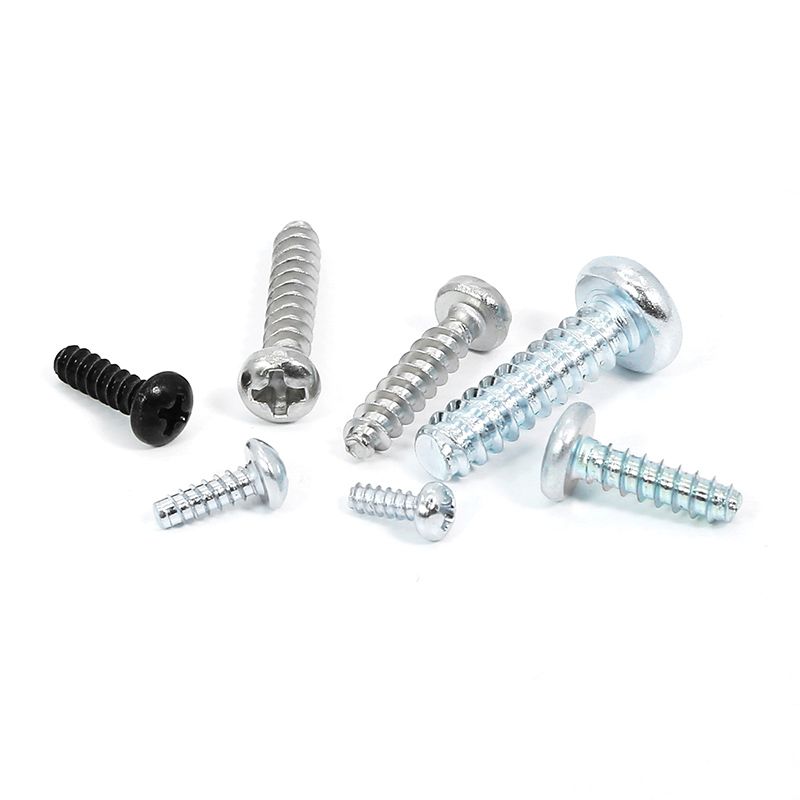
2. fosfatmine
Põhipõhimõte on see, et fosfatmine on suhteliselt odavam kui galvaniseerimine, kuid selle korrosioonikindlus on halvem kui galvaniseerimine. Pärast fosfaati tuleks õli rakendada ja selle korrosioonikindlus on tihedalt seotud rakendatud õli jõudlusega. Näiteks pärast fosfaati, üldise roostevastase õli pealekandmist ja neutraalse soolapihusti testi läbiviimist ainult 10-20 tundi. Kvaliteetse roostevastase õli pealekandmine võib võtta kuni 72–96 tundi. Kuid selle hind on 2-3-kordne üldine fosfaatõli.
Kinnitusvahendite jaoks on kahte tüüpi fosfaatide tüüpi, tsingipõhine ja mangaanipõhine fosfaat. Tsingipõhisel fosfaadil on parem määrimisvõime kui mangaanil põhineval fosfaadil ja mangaanil põhineval fosfaadil on parem korrosioonikindlus ja kulumiskindlus kui tsingiplaadil. Seda saab kasutada temperatuuridel vahemikus 225 kuni 400 kraadi Fahrenheiti (107-204 ℃). Eriti mõne olulise komponendi ühendamiseks. Nagu mootori ühendusvarda poldid ja pähklid, silindripea, peamine laager, hooratta poldid, rattapoldid ja pähklid jne.
Kõrge tugevusega poldid kasutavad fosfaati, mis võib vältida ka vesiniku omastamise probleeme. Seetõttu kasutavad tööstusvaldkonna poldid üle 10,9 -aastased poldid, mis on tavaliselt fosfaadi pinna töötlemisel.
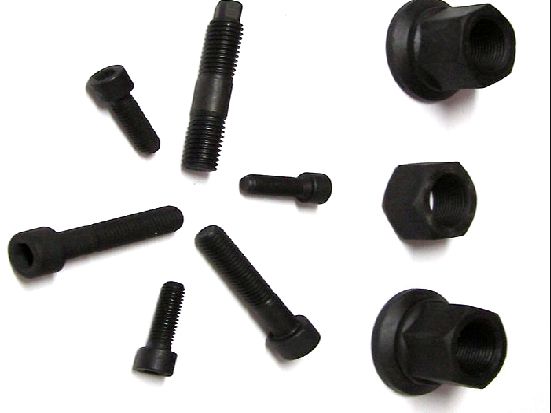
3. Oksüdatsioon (mustandamine)
Blackening+Oiling on populaarne kattekiht tööstuslike kinnitusdetailide jaoks, kuna see on kõige odavam ja näeb hea välja enne kütusekulu. Selle mustuse tõttu pole sellel peaaegu rooste ennetamise võimet, nii et roosteb kiiresti ilma õlita. Isegi õli juuresolekul võib soolapihusti test kesta ainult 3-5 tundi.
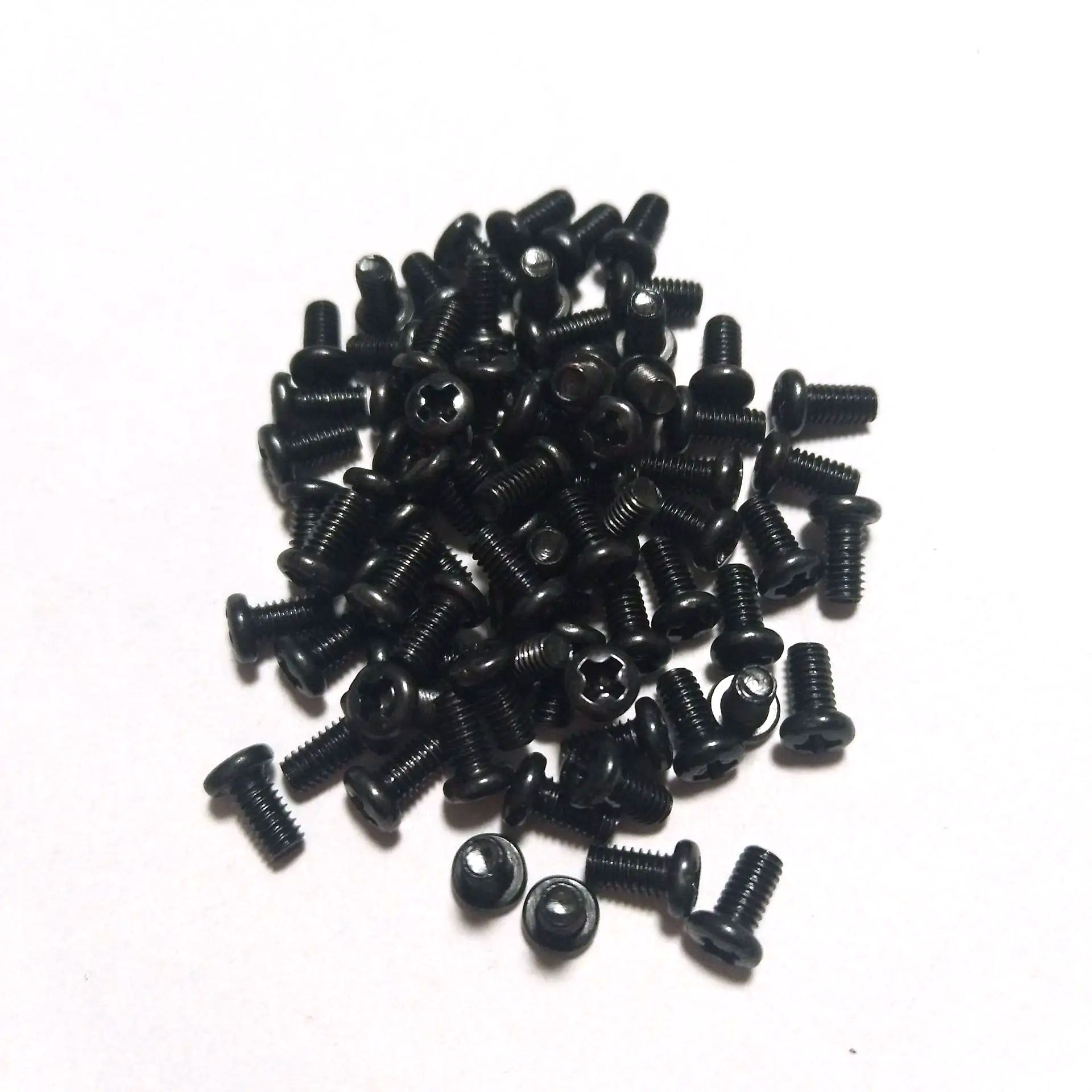
4. Elektroplatsiooniline partitsioon
Kaadmiumiplaadil on suurepärane korrosioonikindlus, eriti mere atmosfääri keskkonnas, võrreldes teiste pinnaravidega. Jäätmevedeliku töötlemise kulud kaadmiumi elektropleksiooni protsessis on kõrge ja selle hind on umbes 15-20 korda suurem kui tsink. Seega ei kasutata seda üldistes tööstusharudes, ainult konkreetsetes keskkondades. Õlipuurimisplatvormide ja HNA lennukite jaoks kasutatavad kinnitusdetailid.
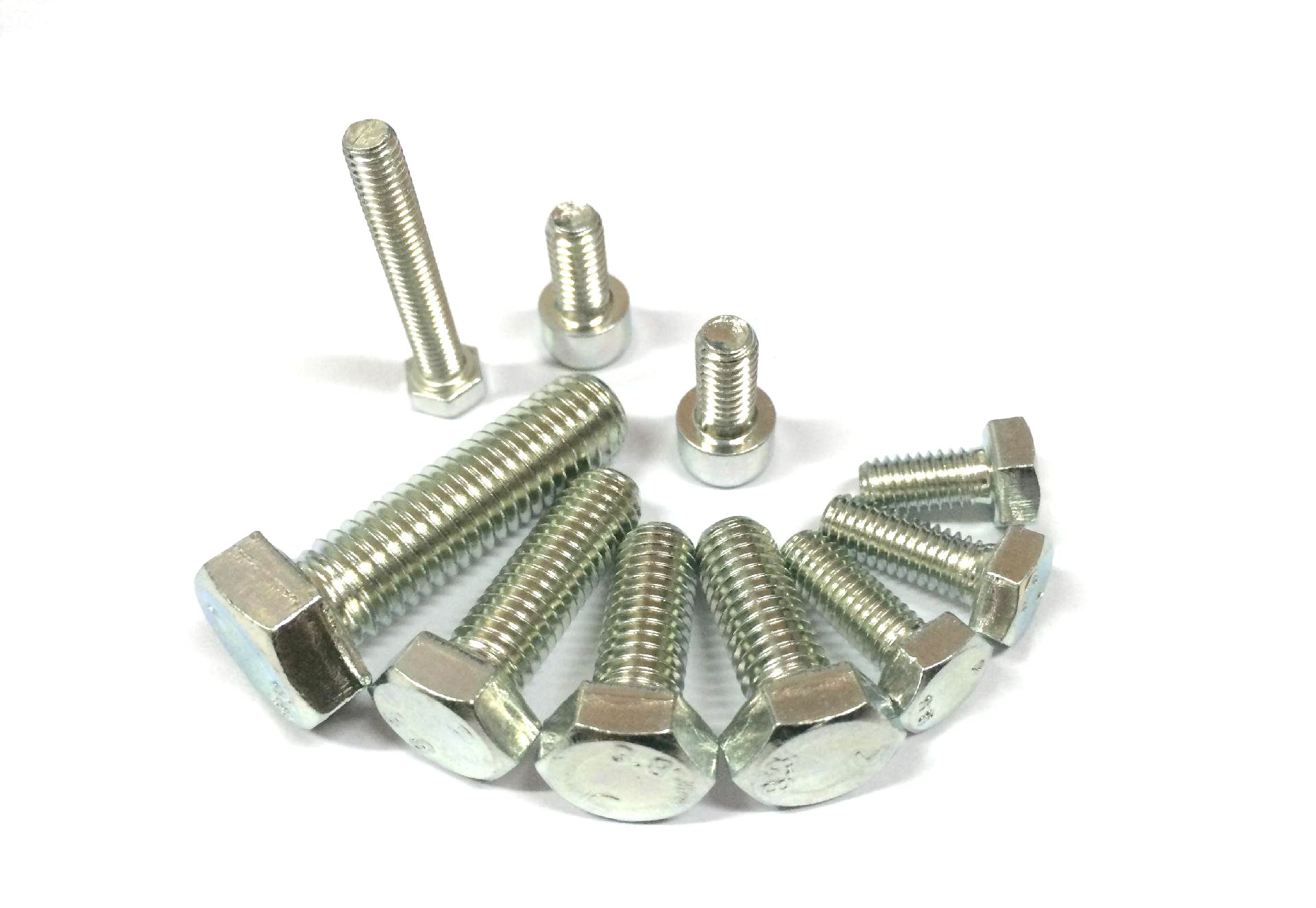
5. kroomi plaadistamine
Kroomi kattekiht on atmosfääris väga stabiilne, värvi muutmine ja läige kaotamine ning hea kõvadus ja hea kulumiskindlus. Kroomiplaadi kasutamist kinnitusdetailidel kasutatakse tavaliselt dekoratiivsetel eesmärkidel. Seda kasutatakse harva tööstusväljadel, millel on kõrge korrosioonikindlus, kuna head kroomitud kinnitusdetailid on sama kallid kui roostevaba teras. Ainult siis, kui roostevabast terasest tugevus on ebapiisav, kasutatakse selle asemel kroomitud kinnitusdetailid.
Korrosiooni vältimiseks tuleks enne kroomitud plaatimist kõigepealt vask ja nikkel pindada. Kroomi kattekiht talub kõrget temperatuuri 1200 kraadi Fahrenheiti (650 ℃). Kuid on ka vesiniku omastamise probleem, mis sarnaneb elektrogalvaniseerimisega.
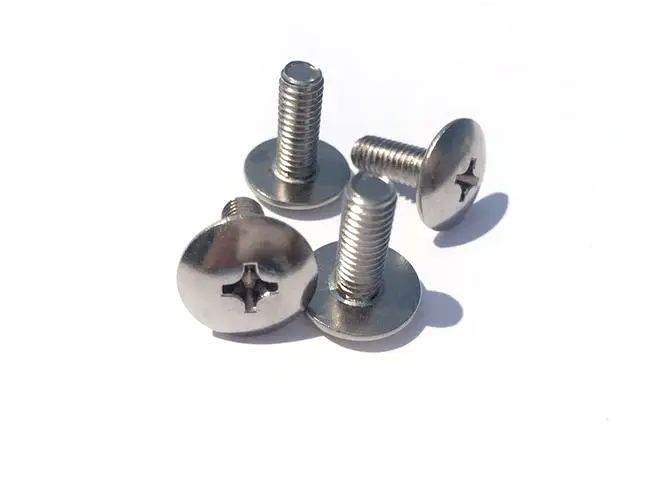
6. nikliplaatimine
Kasutatakse peamiselt piirkondades, mis nõuavad nii korrosioonivastast kui ka head juhtivust. Näiteks sõidukite akude väljaminevad klemmid.
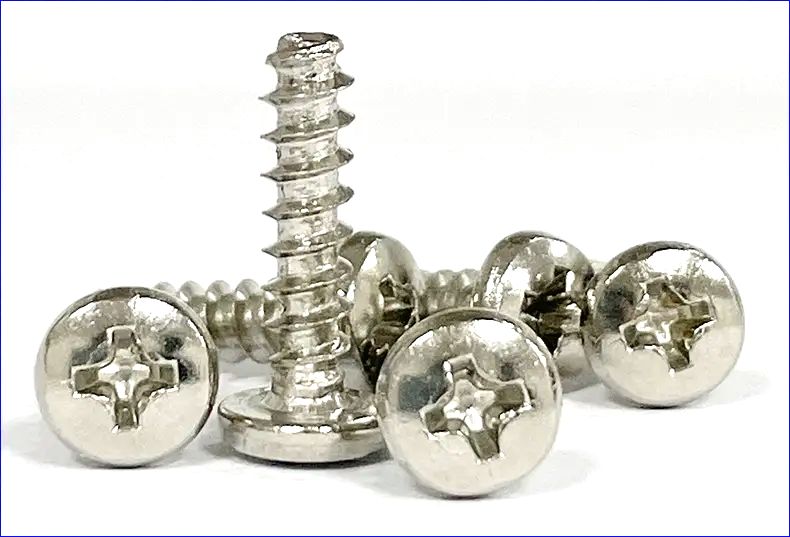
7.
Kuum kastmine galvaniseerimine on vedelikule kuumutatud tsingi termiline difusioonikate. Katte paksus on vahemikus 15 kuni 100 μm. Ja seda pole lihtne kontrollida, kuid sellel on hea korrosioonikindlus ja seda kasutatakse sageli inseneritöös. Kuuma dip -galvaniseerimisprotsessi ajal on tõsine reostus, sealhulgas tsingijäätmed ja tsingi auru.
Paksu katte tõttu on see tekitanud raskusi kinnitusdetailides sisemise ja väliste niitide kruvimisel. Kuum-dip-galvaniseeriva töötlemise temperatuuri tõttu ei saa seda kasutada kinnitusdetailide jaoks, mis ületavad klassi 10,9 (340 ~ 500 ℃).
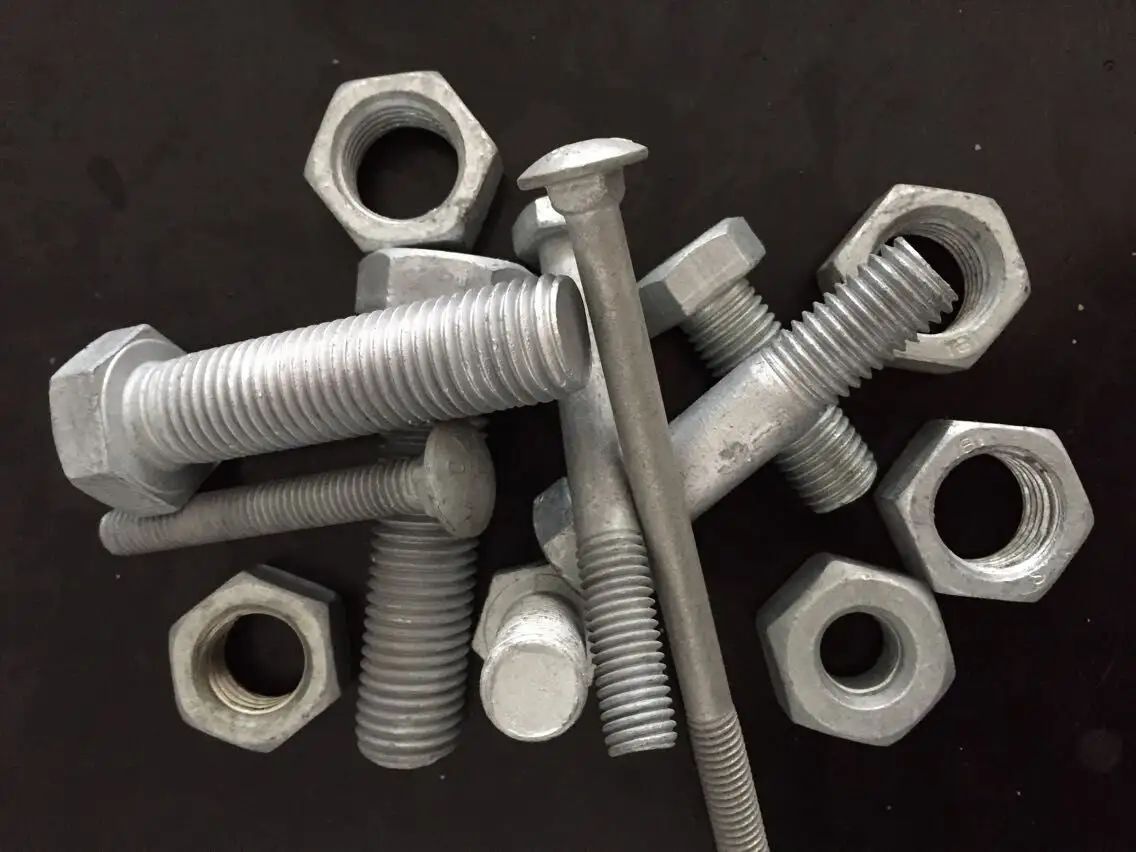
8. tsingi infiltratsioon
Tsinki infiltratsioon on tsingipulbri tahke metallurgiline termiline difusioonikate. Selle ühtlus on hea ja ühtlast kihti saab nii keermetes kui ka pimedates aukudes. Plaatimise paksus on 10–110 μm. Ja viga saab juhtida 10%-l. Selle sidumisjõud ja korrosioonivastane jõudlus substraadiga on parimad tsingikatete (näiteks elektrogalvaniseerimine, kuum-dip-galvaniseerimine ja daakromet). Selle töötlemisprotsess on reostusvaba ja kõige keskkonnasõbralikum.
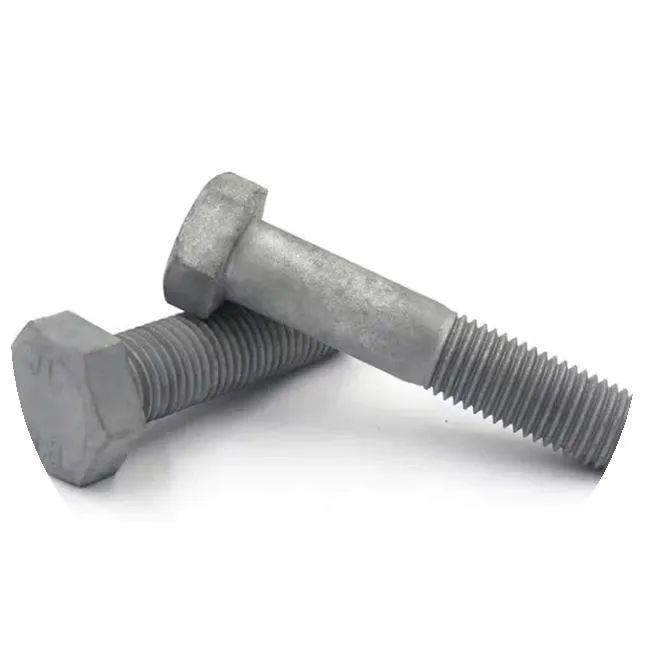
9. Dacromet
Vesiniku omastamise probleemi pole ja pöördemomendi eelkoormuse järjepidevuse jõudlus on väga hea. Kaalumata kroomi ja keskkonnaprobleeme, on Dacromet tegelikult kõige sobivam ülitugevate kinnitusdetailide jaoks, millel on kõrge korrosioonivastane nõue.
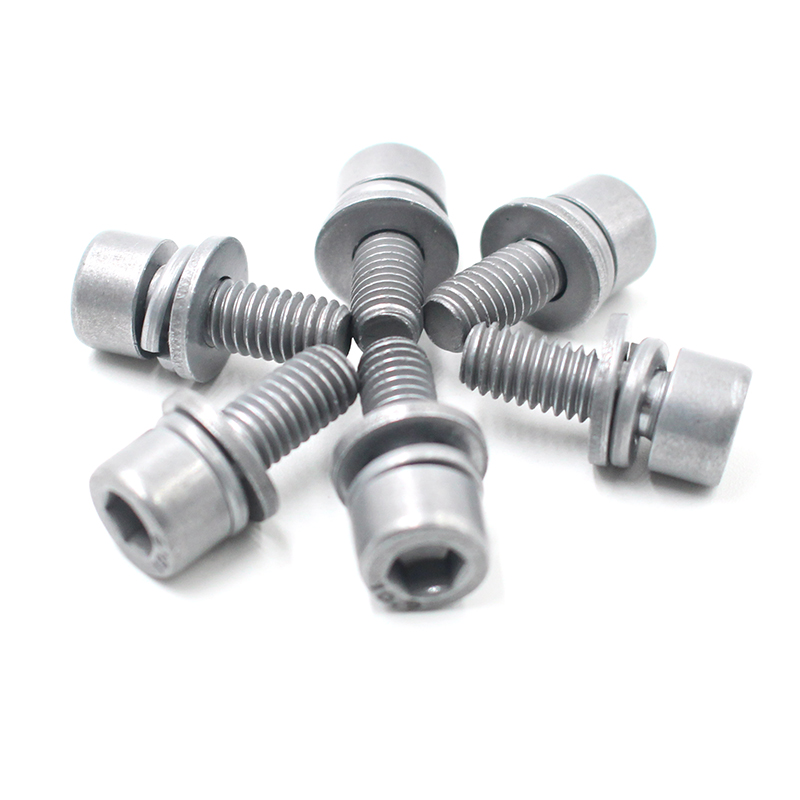
Postiaeg: 19. mai 20123